Hydraulic Cylinder Chroming Service
When your equipment works hard, your hydraulic systems take the brunt of it. That’s why we offer advanced in-house cylinder rod chroming service to restore and protect your components with precision and care. Using state-of-the-art technology, we apply wear-and corrosion-resistant coatings that extend rod life and keep your equipment running longer—no matter the manufacturer or working application.
Our solutions are built for demanding industries like construction, mining, marine, and forestry—where durability matters most. We are equipped to work on industrial equipment as well, including aerial lifts, bucket trucks, cranes, forklifts, farm tractors, shipyard equipment, manufacturing machines, and more. Schedule a service today to get started.
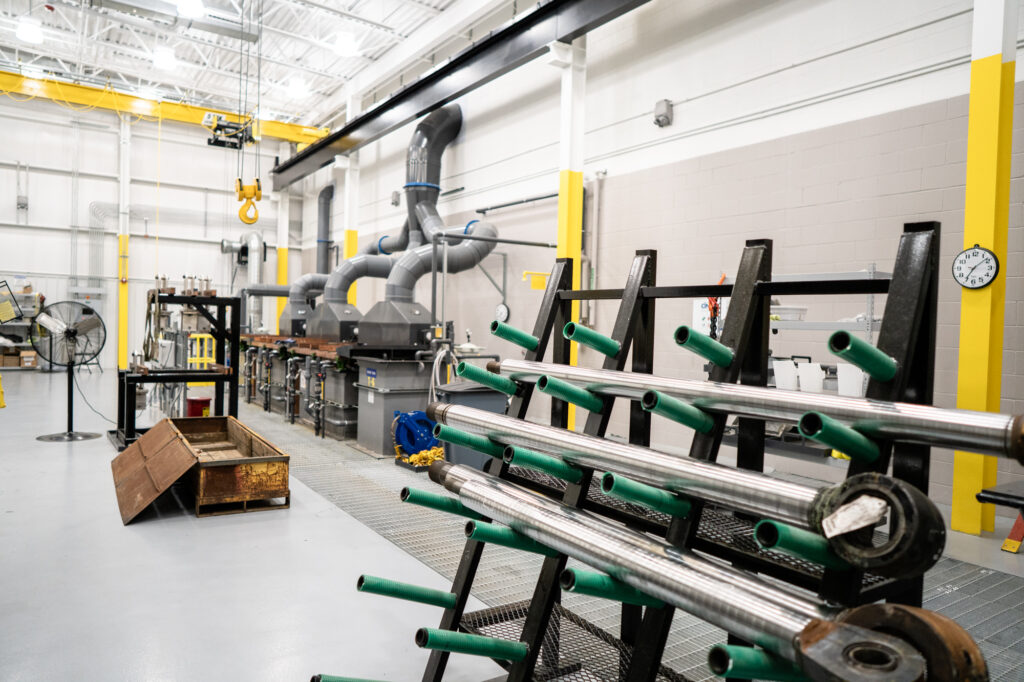
Fast, In-House Turnaround You Can Count On
We understand that downtime costs you money, which is why fast, reliable turnaround is at the core of our service. With our fully equipped, in-house chrome and coating shops, we can handle the entire hydraulic cylinder rod repair process under one roof, getting your equipment back to work quickly.
Here’s How Our Chroming Process Works
- Chrome Removal & Inspection
It all starts with stripping the old chrome from the rod in a dedicated removal tank. Once clean, the rod is thoroughly inspected for damage. - Welding & Machining Repairs
If we find any deep scratches, wear, or other imperfections, our expert welding and machine shop steps in to make precise repairs — ensuring the rod is restored to spec before chroming. - Surface Preparation
After repairs, the rod undergoes a reverse etching process that opens the material’s pores at the microscopic level. This critical step ensures the new chrome layer bonds tightly and uniformly. - Chroming Application
The rod is then placed in our chroming tank, where a technician carefully applies a consistent layer of high-quality chromium. The rod is monitored throughout the process to ensure proper thickness and coverage. - Reassembly & Final Testing
Once chromed, the rod returns to our hydraulic shop for reassembly. It’s tested to meet performance standards before it’s returned to you — ready for work.
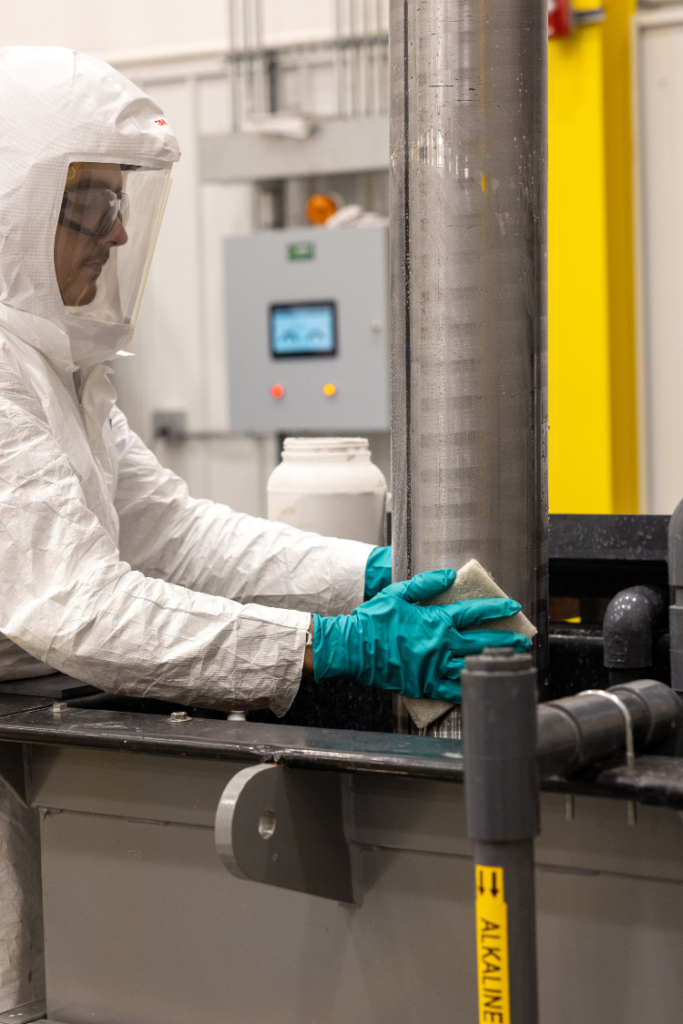
High Velocity Oxygen Fuel (HVOF) Thermal Spray Coating
Applied at our Baltimore Reman location, HVOF thermal spray coatings are increasingly used across industries such as aerospace, marine, oil & gas, and more, thanks to their high performance and reliability. As an alternative to Electroplated Hard Chrome (EHC), HVOF coatings offer a range of benefits for certain specialized applications:
- Excellent Wear Resistance
HVOF 6P combustion powder coatings demonstrate strong resistance to sliding and abrasive wear, making them ideal for high-friction environments. - Enhanced Corrosion Protection
In extended saltwater exposure testing, HVOF coatings have shown a high level of resistance to corrosion, making them suitable for harsh operating conditions. - Strong Impact Resistance
Impact tests using ball and gravel methods indicate that HVOF coatings can provide durable surface protection under demanding mechanical stress. - Maintained Fatigue Strength
Parts coated with HVOF have shown the ability to retain or improve fatigue strength, which can be beneficial in components subjected to cyclical loading. - Cost and Environmental Considerations
For some applications, HVOF may offer long-term cost efficiency and environmental benefits, depending on operational and regulatory factors.